导 热 油 使 用 手 册
深圳市特种设备安全检验研究院 张居光
一、 主要术语
1.导热油
●以液相或气相进行热量传递的物质。
●
导热油即
有机热载体,又名
热传导液,分矿物油型和合成型
●矿物油型热传导油:石油加工过程中某段馏分经精制后调配功能添加剂制得。
●合成型导热油:以化工或石油化工产品为原料,经有机合成工艺制得。
2.开式和闭式传热系统
●膨胀油槽直接与大气相通的传热系统称为开式传热系统。
●膨胀油槽采用惰性气体(一般为氮气)封闭的传热系统称为闭式系统。
3.最高使用温度
●根据导热油分类标准(GB/T 7631.12-94),产品类别按最高使用温度划分。最高使用温度采用热稳定性试验法确定。最高使用温度系指某产品经热稳定性试验测得变质率不大于10%所对应的温度,最高实际使用温度系指加热器出口处测得的主流体最高平均温度。
●一般情况下,任何一种导热油产品,尤其是矿物油型产品,其最高实际使用温度应较其最高使用温度至少低20℃,以保证一定的使用寿命及较好的安全性和经济性。
4.热稳定性
●从试验角度讲,热稳定性是在规定的试验温度及时间条件下,导热油在隔绝空气状态下,因受热作用(热裂解和热聚合)而表现出的稳定性。
●对某一特定产品来说,其热稳定性由组成、纯度、精制深度、馏程范围等因素决定。
●热裂解反应,生成气体和低沸物。
●热聚合反应,生成高沸物和高分子粘稠状聚合物,最后形成沉渣。
●导热油在实际运行中,热裂解和热聚合反应会伴随始终,其组成无时无刻不在发生变化,是不可避免的,但其程度可以控制。
●热氧化反应,生成低分子或高分子的醇、醛、酮、酸等酸性组分,并进一步生成胶质、沥青质等粘稠物质,最后形成沉渣。
●热氧化是非正常情况引起的,一旦发生,会产生很坏的影响(加速热裂解和热聚合反应,酸性物质造成设备腐蚀和泄漏,粘度迅速增大,传热效率降低,造成过热和炉管结焦),但可以通过加入高温导热油复剂避免或延缓。
二、 产品牌号
参考国内按最高使用温度划分产品牌号的方式,考虑到不同使用温度的要求和对原料初馏点的限制,导热油按最高使用温度将L-QB和L-QC产品划分为L-QB240、L-QB280、L-QB300和L-QC320四个牌号。其中L-QB240最高使用温度为240℃,常用于小型电加热采暖装置;L-QB280、L-QB300和L-QC320一般在工业传热系统中使用,最高使用温度分别为280℃、300℃和320℃;L-QD一般用于工业传热系统中,产品类型为合成型,最高使用温度可高于320℃。其牌号为L-QDXXX,其中XXX为高于320℃的某一温度。
三、 主要技术指标
1. 热稳定性
热稳定性是导热油区别于其他油品的重要使用性能,标准号为SH/T 0680-1999。
该方法是在一定试验温度(产品标准中规定的最高使用温度)下,将试样隔绝空气加热至规定时间,然后观察并记录其外观;计算出气相分解产物质量;对加热前后的试样进行气相色谱分析,通过模拟蒸馏曲线确定试样生成的低沸物和高沸物含量;称取一定量加热后的试样,在球管蒸馏器中测定不能蒸发的产物含量;最后计算出试样的变质率。
L-QB和L-QC的热稳定性指标为在其最高使用温度下加热720h,总变质率不大于10%;L-QD的热稳定性指标为,在其最高使用温度下加热1000h,总变质率不大于10%。
经对国内各种类型产品进行评定,矿物油型产品的最高使用温度不超过320℃,这符合国内目前的应用实际。
2 初馏点
对于在开式系统中使用的导热油来说,初馏点是一项重要指标。实际应用中发现,有些初馏点很低的产品在开式系统中使用,造成操作不平稳,挥发损耗相当大,年补充量可达50%以上。这不仅使用户承担了不必要的经济损失,而且由于轻组分挥发,造成粘度增高,传热效率下降,加热设备超温和炉管结焦等一连串的问题,降低了传热系统的整体安全性和导热油的经济性。
在大量试验基础上,规定在开式设备中使用的导热油的初馏点不低于其最高使用温度,试验方法采用模拟蒸馏气相色谱法。
3 闪点和自燃点
闪点和自燃点是导热油的安全性能指标,预示运行中的导热油遇明火发生燃烧或在空气中自燃的倾向。规定闭口闪点不低于100℃,自燃点为报告。
根据对市场采样和生产厂送样的分析测试,闭口闪点不低于100℃的要求全部可以达到,这是一项基本的安全要求。而开式系统使用的产品,如闪点过低,可能是安全的隐患。实际应用中,设备的膨胀罐因导热油闪点和初馏点过低而着火的事故时有发生,因此还应对开口闪点合理控制。L-QB240、L-QB280、L-QB300和L-QC320的开口闪点分别为160℃、180℃、190℃和200℃。
4 水分
导热油中的水分在加热过程中会气化,引起急剧膨胀,造成操作不平稳,因此导热油中的水分应严格控制。规定水分为不大于500mg/kg,试验方法为微量水测定法。因L-QB240主要用于小型电热取暖装置,对水分要求更为严格,本标准规定其水分含量为不大于200mg/kg,其它各牌号为不大于500 mg/kg,试验方法为微量水测定法。
5 倾点
倾点和低温粘度决定了导热油的低温流动性。考虑到我国低粘度润滑油基础油的倾点指标为不高于-9℃。如有特殊低温要求,可与生产者商定协议指标。
6.硫含量
硫含量与产品的精制深度相关。导热油如硫含量较高,使用中可能造成设备的腐蚀。指标为不大于0.2%。
7.氯含量
氯含量与产品毒性相关。在国外,曾使用热稳定性非常好的氯代烃类化合物作为热载体或变压器油,这些氯化物有很强的致畸性。指标为不大于0.01%。
8.中和值和铜片腐蚀
中和值和铜片腐蚀反映产品的精制深度,与设备腐蚀情况相关。
中和值指标为不大于0.2%。铜片腐蚀指标为在100℃,3h条件下,评级为1级。
9.密度
密度是反映产品构成的指标,与其传热性能相关。
10. 残炭、灰分
残炭和灰分是反映原料精制深度的指标。残炭和灰分较高的产品,稠环芳烃等重质成分含量较高,产品颜色较深,热稳定性较差。
11.馏程
馏程是反映产品的沸点范围的指标。蒸馏切割越窄,重组分越少,热稳定性也越好。
12.运动粘度
运动粘度反映液体的运动阻力,决定了在一定温度下液体的流动性和泵送性。导热油对运动粘度的要求,是在满足热稳定性、初馏点、闪点等重要指标的同时,具有较低的粘度,很好的高温和低温流动性。
四、 选购导热油注意事项
●
考察产品最高使用温度的真实性—— 经专门部门采用热稳定性试验方法确定,即在最高使用温度下进行试验后外观透明,无悬浮物和沉淀,总变质率不大于10%所对应的温度。通过与新标准作对照,分析产品说明书的真实性。尤其要了解其规定的最高使用温度是如何确定的,有无权威机构的检测报告。
●
考察产品的蒸发性和安全性——开口闪点符合标准指标要求,初馏点不低于其最高使用温度,馏程比较窄,自燃点比较高。
●
考察产品的精制深度——外观为浅黄色透明液体,储存稳定性好,光照后不变色或出现沉淀。残炭不大于0.1%,硫含量不大于0.2%。
●
考察产品的低温流动性——根据用户所处地区和设备的环境温度情况,选择适宜的低温性能。QB和QC倾点不高于-9℃,低温运动粘度(0℃或更低温度)相对比较低。
●
考察产品的传热性能——具有较低的粘度、较大的密度、较高比热容和导热系数。
●选用正规生产企业生产的产品。有条件可实地考察其生产设备和检测手段的完善情况。
五、导热油的使用
1、导热油作废技术指标
答:矿物型导热油报废有以下四方面指标,可供参考:
①粘度变化大于15%,应引起注意;
②闪点变化大于20%,应引起注意;
③酸值大于0.5mgKOH/g,应引起注意;
④残炭达到1.5%,应引起注意。
在对运行中的导热油进行测试时发现,粘度因受分解和聚合的共同影响,变化并不规律;酸值在氧化初期逐渐增大而后反而下降;闪点是说明油品运行安全性的重要指标;残炭则一直呈上升趋势,开始缓慢,而后数值增长明显加快。 总之,对上述指标不能孤立地去看其中某一项,必须综合分析,做出判断。
2、 不同牌号的导热油的混用
答:从导热油的使用性能看,纯度越高、馏程范围越窄,其热稳定性越好。一个混合物的热稳定性是由其中热稳定性较差的组分决定。因此,导热油可否混用必须遵循科学的方法,即采用SH/T 0680-1999“导热油热稳定性测定法”试验方法进行评价,根据试验分析数据做出判断。
3、 使用过的导热油可以再生后重新使用,何谓再生
答:所谓再生,是将使用到一定程度但尚未报废的导热油经适当处理,使之达到原产品的指标。处理方法一般是经减压蒸馏除掉高沸物和低沸物,然后精制、脱色。
合成型导热油的价格较高,使用周期较长,延长其使用寿命的有效方法是定期取出部分进行再生。如某化纤公司的聚酯装置,开车3年后每年取出总量的1/3进行再生,这样循环使用可大大减缓其变质速率。
矿物型导热油的价格便宜且加有一定数量的添加剂,一般再生后不再用作导热油。用户可根据使用情况进行部分更换,同样可减缓其变质速率。
应该注意的是,部分再生或部分更换应根据日常检验,掌握好时机。如果导热油已严重老化,可能造成设备结焦,必须彻底更换。
4、 液相炉中膨胀槽的作用是什么
答:在液相加热系统中,膨胀槽的设置必不可少。膨胀槽通常设置在系统的最高点,因此除容纳导热油受热膨胀量外,还兼有其他重要功能,如新填装产品中轻组分和运行中产生的低沸物的排空、补充蒸发及操作损耗、氮气密封等。
在实际使用中常有一些装置的膨胀槽必须氮封。膨胀槽氮封的作用之一是防止导热油因接触空气而氧化,另外可施加一定压力,保持液相运行。
一般来说,导热油的氧化可通过系统的设置、操作及加入高温抗氧剂加以控制,如升高膨胀槽的位置、采用小口径膨胀管以防冷热油产生对流、控制膨胀槽温度低于60℃。如导热油的初馏点高于系统的最高使用温度,则可以不采用氮封;如导热油的初馏点低于系统的最高使用温度,就可能有部分组分汽化造成泵的气蚀和较大的蒸发损耗,这种情况必须采用氮封。
5、 日常操作中,怎样来延长导热油使用寿命
答:如果系统设计合理、配置适当、导热油产品质量符合SH/T 0677-1999“导热油”标准,延长使用寿命的关键在于日常的操作管理,以下几点可供参考:
(1)开车之前,对操作和管理人员进行培训,使之掌握科学方法,有能力对异常情况进行处理。
(2)严格遵守操作规程,保证工艺要求的主流体温度不超过所选导热油的最高使用温度,同时还要对导热油的流速、流量和进出温差进行严格控制,避免因局部过热而导致裂解和结焦。
(3)防止空气、水和其他污染物进入系统。
(4)经常检查旁路过滤器压力降,及时清洗或更换滤芯,保证过滤效果。
(5)不采用氮封的加热系统,膨胀槽温度应控制在60℃左右,不要超过80℃。
(6)根据使用情况,定期取样化验,掌握油品的变质情况,以便及时采取措施。
6、 导热油炉容易发生的安全事故
答:导热油为可燃性有机物,具有着火和爆炸的潜在危险,分析事故原因,主要有以下几种可能:
(1)法兰连接或泵密封处发生泄露,如不及时维修,遇明火会着火。
(2)加热器管线因局部过热,管内结焦或超压使炉管破裂,泄露物进入明火区随时可能发生事故。
(3)导热油泄露进入生产设备,遇氧化剂或催化剂会剧烈燃烧,甚至产生爆炸。
(4)膨胀槽与空气接触,高温氧化导致自燃。
(5)泄露的导热油进入管线保温层,逐渐氧化产生低自燃点组分,可能导致自燃。
(6)气相系统中,泄露的导热油形成气雾,在空气中达到一定浓度时会燃烧或爆炸。
(7)气相系统中如有水混入,因体积剧烈膨胀而爆炸。
(8)导热油变质过快,不溶性炭粒造成密封损坏而导致泄露。
从系统配置上应选用优质油泵、阀门和密封垫。操作管理上要及时维修,避免机械故障和错误操作。
7、 选用导热油时应该注意的问题
答:在选择导热油前,首先应确定适当的加热工艺流程,最好委托专业部门做系统设计。如果系统已经结焦,需要再次选油,则应认真找出结焦原因,对系统设计、部件设置和操作管理中的问题进行纠正,同时还要对系统进行认真清洗。
目前,我国导热油产品执行SH/T 0677-1999“导热油”标准,用户在购买前应注意以下问题:
(1)考察产品最高使用温度的真实性-经石科院采用热稳定性试验方法确定,即在最高使用温度下进行试验后外观透明,无悬浮物和沉淀,总变质率不大于10%所对应的温度。通过与新标准作对照,分析产品说明书的真实性。尤其要了解其规定的最高使用温度是如何确定的,有无权威机构的检测报告。
根据国际标准化分类,矿物型导热油的最高使用温度不超过320℃ ,目前多数该类油品的最高使用温度为300℃。
(2)考察产品的蒸发性和安全性-闪点(开口)符合标准指标要求,初馏点不低于其最高使用温度,馏程比较窄,自燃点比较高。
(3)考察产品的精制深度-外观为浅黄色透明液体,储存稳定性好,光照后不变色或出现沉淀。残炭不大于0.1%,硫含量不大于0.2%。
(4)考察产品的低温流动性-根据用户所处地区和设备的环境温度情况,选择适宜的低温性能。QB和QC倾点不高于-9℃,低温运动粘度(0℃或更低温度)相对比较低。
(5)考察产品的传热性能-具有较低的粘度、较大的密度、较高比热容和导热系数。
(6)选用正规生产企业生产的产品。有条件可实地考察其生产设备和检测手段的完善情况。
8、 在导热油取样化验时,怎样才能获得有代表性的样品
答:为获得有代表性的导热油样品,应在装置的同一部位相同条件下取样。建议取样点在接近加热器的流动线上,并尽量不使低沸物跑掉,以免影响闪点和初馏点的测定。
9、 液相炉系统中安装旁路过滤器的必要性
答:导热油在运行中由于热裂解和热聚合会产生胶质、沥青质和细小炭粒,这些物质数量逐渐增加会导致设备结焦和一系列操作问题。
通常在泵前设置的金属丝网过滤器只能除掉机械杂质和污物。如在系统中安装一旁路过滤器,则可在不停车的情况下随时将胶质、沥青质和炭粒滤除。
从延长导热油使用寿命的角度考虑,最好在开车前就设置合适的旁路过滤器,并连续使用。如果油品已经变质,可及时加设旁路过滤器,采用不同孔径的滤芯,从粗滤到细滤逐渐更换。
10、 导热油使用过程中定期取样化验的必要性,化验项目有哪些
答:运行中定期检验的目的是了解油品内在质量的变化,并由此发现系统设计、操作管理及导热油自身的质量问题,及时纠正以延长其使用寿命。从以下检验项目可说明运行中导热油的变质情况:
(1)馏程:馏程的变化表明导热油分子质量的变化,国外近年来采用气相色谱法,经与新油的馏程进行比较,以高沸物和低沸物含量表明导热油发生裂解和聚合的程度。
(2)粘度:粘度的变化表明导热油分子质量和结构的变化。裂解使粘度下降,而聚合和氧化使粘度上升。这些变化对高温范围的粘度影响很小,但对低温粘度影响较大,因此对寒冷地区和伴有冷却的操作工艺来说,低温粘度增长应引起重视。
(3)酸值:酸值的变化表明导热油的老化程度。酸值上升通常是油品发生氧化所致,主要发生在膨胀槽不采用氮封的系统中。但当老化到一定程度时,可溶性有机酸可能进一步聚合生成高分子氧化产物,这时酸值又可能下降。因此,要注意从酸值的变化趋势判断油品的老化程度。
(4)残炭:残炭是运行中的导热油经蒸发和裂解后留下的残炭量。在运行中残炭量往往随时间呈不断上升的趋势,可说明高分子炭状沉积物形成的倾向和老化的程度。
近年来,国外常测定丙酮或戊烷不溶物,包括油不溶物和因裂解、聚合而产生的树脂状物。因该方法未经蒸发和热解,可准确说明油品中不溶物的含量。
(5)闪点:闪点是主要的安全性指标,说明高挥发性产物和可燃性气体形成的可能性。闪点下降过多可能成为事故的隐患。
一般通过以上检验项目对导热油的变质情况进行综合判断。
11、 导热油炉什么时候应该进行化学清洗
答:所谓化学清洗,是采用化学药剂对系统进行清洗,包括试运转前和运转过程中的清洗。
试运转前应进行系统的除锈操作,虽然会增加投资,但从长远考虑是值得的。有的系统不经除锈就灌入导热油,造成油品在试运转阶段已变成铁锈色,对其寿命影响很大。
运转中的清洗是指清除由于导热油在加热器和循环管线中产生的积垢。积垢过程分为3步:
(1)热裂解和热聚合产物首先形成聚合的高碳粘稠物,附着于管壁,这类物质可通过化学清洗去除。
(2)高碳粘稠物进一步形成不完全石墨化沉积物,化学清洗只对尚未碳化的部分有效。
(3)完全形成石墨化焦炭。对这类物质化学清洗已不解决问题,国外多采用机械清洗。由于国内机械清洗的专用器具尚未开发,这种情况下只能更换炉管。
因此国内有关专家建议,使用中应经常检查,在形成的高碳粘稠物尚未碳化时,用户可购买化学清洗剂进行清洗。
六、导热油结焦的形成与防止
1、 结焦的形成
导热油在传热过程中主要发生三种化学反应:热氧化反应、热裂解和热聚合反应。结焦产生于热氧化反应和热聚合反应。
热聚合反应因导热油在加热系统运行过程受热而发生,该反应会生成稠环芳烃、胶质和沥青质等大分子高沸物,其逐渐沉积于加热器和管路表面,形成结焦。
热氧化反应主要因开式加热系统膨胀槽内的导热油接触空气或参与循环而发生,该反应会生成低分子或高分子的醇、醛、酮、酸等酸性组分,并进一步生成胶质、沥青质等粘稠物质,最后形成结焦;热氧化是非正常情况引起的,一旦发生,会加速热裂解和热聚合反应,使粘度迅速增大,传热效率降低,造成过热和炉管结焦。产生的酸性物质还会造成设备腐蚀和泄漏。
2、 结焦的危害
导热油在使用过程中产生的结焦会形成隔热层,致使传热系数下降、排烟温度升高、燃料消耗增大;另一方面由于生产工艺所需温度保持不变,加热炉管壁温度会急剧上升,从而引起炉管鼓包、破裂,最终将炉管烧穿,引起加热炉着火、爆炸,造成设备和操作者人身伤害等严重事故。近年来,此类事故屡见不鲜。
3、 结焦的影响因素
3.1、导热油质量
经对以上结焦的形成过程进行分析发现,导热油氧化安定性和热稳定性的高低与结焦速度和数量密不可分。许多着火和爆炸事故是由于导热油的热稳定性和氧化安定性较差,运行过程中引起严重结焦造成的。
3.2、
加热系统的设计及安装
加热系统设计所提供的各种参数及设备安装是否合理,直接影响导热油的结焦倾向。每台设备安装情况不一样,也会影响导热油的寿命。设备安装必须合理,调试时需及时整改,才有利于导热油的寿命延长。
3.3
加热系统的日常操作及维护
不同操作人员因文化程度和技术水平等客观条件不同,即使使用相同的加热设备和导热油,其对加热系统温度和流速等因素的控制水平也不尽相同。
温度是导热油发生热氧化反应和热聚合反应的重要参数。随着温度的升高,这两种反应的反应速度会急剧增加,结焦倾向也随之增大。根据化工原理的有关理论:随着雷诺数的增加,结焦速率减慢。雷诺数与导热油的流速成正比。因此,导热油流速越大,结焦越慢。
4、 减缓结焦的办法
为减缓结焦的形成速度,延长导热油的使用使命,应从以下方面采取措施:
4.1、选择适宜牌号的导热油,定期监测其理化指标变化趋势
导热油根据最高使用温度划分牌号,其中矿物型导热油主要有L-QB280、L-QB300和L-QC320三个牌号,其最高使用温度分别为280℃、300℃和320℃。
应根据加热系统的最高加热温度选择适宜牌号、质量符合SH/T 0677-1999 “导热油”标准的导热油。目前,一些市售导热油推荐的最高使用温度与实际测定结果出入较大,给用户以误导,安全事故时有发生,应当引起广大用户的注意!
应选用由优良热稳定性的精制基础油和高温抗氧剂和抗垢添加剂调配的导热油。其中高温抗氧剂可有效延缓导热油运行过程中的氧化变稠;高温抗垢剂可将炉管和管路中的结焦溶解,使其分散在导热油中,最后通过系统的旁路过滤器将其过滤,保持炉管和管路的清洁。
导热油每使用三个月或半年后,应对其粘度、闪点、酸值和残炭四项指标进行跟踪分析,当其中有两项指标超过规定限值(残炭不大于1.5%、酸值不大于0.5mgKOH/g、闪点变化率不大于20%、粘度变化率不大于15%)时,应考虑添加部分新油或全部换油。
4.2、加热系统合理的设计及安装
导热油加热系统的设计及安装应严格执行国家有关部门制定的热油炉设计规程,以保证加热系统的安全运行。
4.3、规范加热系统的日常操作
导热油加热系统的日常操作应严格执行国家有关部门制定的有机热载体炉安全技术监察规程,随时监测加热系统中导热油的温度和流速等参数的变化趋势。
在实际使用中,加热炉出口处的平均温度应较导热油的最高使用温度至少低20℃。
开式系统的膨胀槽中导热油的温度应低于60℃, 最高温度不要超过180℃。
导热油在热油炉中流速不应低于2.5米/秒,以增加导热油湍动程度,减少传热边界层中滞流底层厚度和对流传热热阻,提高对流传热系数,达到强化流体传热的目的。
4.4、加热系统的清洗
热氧化和热聚合产物首先形成聚合的高碳粘稠物,附着于管壁,这类物质可通过化学清洗去除。高碳粘稠物进一步形成不完全石墨化沉积物,化学清洗只对尚未碳化的部分有效。完全形成石墨化焦炭。对这类物质化学清洗已不解决问题,国外多采用机械清洗。在使用中应经常检查,在形成的高碳粘稠物尚未碳化时,用户可购买化学清洗剂进行清洗。
小总结
1.导热油在传热过程中产生的结焦来源于热氧化反应和热聚合反应的反应产物。
2.导热油的结焦会造成加热系统传热系数下降、排烟温度升高、燃料消耗增大的问题,严重时导致加热炉着火、爆炸和操作者人身伤害等事故的发生。
3.为减缓结焦的形成速度,应选择由优良热稳定性的精制基础油和高温抗氧和抗垢添加剂调配的导热油。对于用户来说,应选择最高使用温度经权威部门检测而确定的产品。
4. 合理设计及安装加热系统、使用过程中应规范加热系统的日常操作,定期对运行中导热油的粘度、闪点、酸值和残炭等项指标进行检测,观察其变化趋势。
5.可采用化学清洗剂清洗加热系统中尚未碳化的结焦。
七、导热油系统由于油品问题发生事故的事例
1 海南某企业导热油系统操作温度为320℃,原使用导热油为XXX-320(矿物油,油品商提供允许使用温度为320℃)。在系统调试过程中,导热油温度尚未达到320℃,即出现明显的过热裂解,同时产生的大量低沸物(气体)由安全阀排出,排出后的可燃气体进入地沟,遇电器设备动作打火,引发数次燃烧。该油品使用仅20天,经检验证明已达到报废条件。
2河南某企业导热油系统操作温度为270℃,原使用导热油为XX-300(矿物油,油品商提供允许使用温度为300℃)。该系统投入操作后半年,经常发现膨胀罐排气口有大量气体携带油滴喷出,罐体保温层被油浸透,且罐内导热油温度很高,最后导致保温层数次着火燃烧。经检验证明,该油品的热稳定性较差,由于过热超温产生的大量低沸物(气体)导致了事故的发生。
3 上海某中日合资企业导热油系统操作温度为345℃,原使用日本产导热油为XXX-1400(合成油,油品商提供允许使用温度为350℃)。该系统投入操作后,经常发现膨胀罐排气口有大量气体携带油滴喷出,导热油粘度变化很大,以致停车检修后无法再次启动,必须在停车前将系统导热油排出,并且每三个月更换一次新油后方能投入运行,后致使导热油加热炉结焦报废。经检验证明,该油品在此温度下热稳定性不够,导致导热油严重过热裂解。
4宁夏某企业导热油系统操作温度为260℃左右,原使用导热油为XXX-300(矿物油,油品商提供允许使用温度为300℃)。该系统在使用中发现导热油严重过热裂解,但未能引起操作者重视,后发生加热炉受热炉管内严重结焦,导致炉管过热而爆管,导热油喷入炉膛,引起加热炉爆炸,造成设备和操作者人身伤害的严重事故。
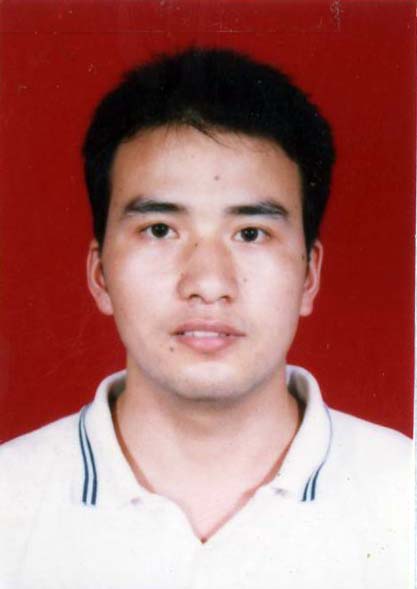
【编者按】作者:张居光、1978年出生于湖南,华南理工大学应用化学专业硕士研究生,现在深圳市特种设备安全检验研究院负责锅炉介质检验和金属材料理化检验,深圳市质监局特种设备专家组成员。此文为作者2008年新作,现征得作者本人同意,在协会网站上发表,特致谢意。